Category
- Products
-
- FAQ
- Contact us
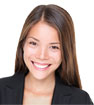
AC Drive Manufacturer
Home » Applications » AC drives on condensing pump of power generator
AC drives on condensing pump of power generator
This application introduces the application of AC drive reform on Condensing pump in 300MW power plant, states the operation mode and energy saving effect after the reform.
The total capacity is 8 × 300MW. Steam turbine unit is produced by Dongfang factory. The condensing system of 5, 6, 7, 8 are medium pressure system, equipped with 9LDTNA-5UA-type condensing pump made by Shenyang pump factory. The motor YLST500-4 type is made by Xiangtan Electrical Machinery Factory.
Condensing pump parameters and diagram
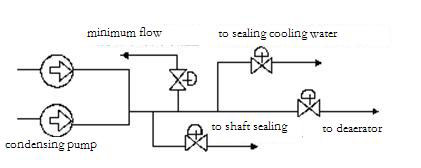
The condensing water mainly keeps the stability of deaerator water level by adjusting inlet gate, supplies mechanical seal cooling water to pump, low pressure axletree of steam turbine and other auxiliary equipments, also to other low pressure bypass, spray cylinder, the cold water tank inside.
Purpose
(1) The condensing water is medium pressure system. The pressure is not lower than 2.6Mpa when load is 300MW. Pressure is higher when opening is small during low load operation, which causes higher pressure. Gate opening control causes low economy. Even at full load, the opening is only about 30%, and much smaller at low-load.
(2) The high pressure condensing water causes the pipe a big vibration, the minimum flow adjustment gate leakage, meanwhile, makes the cooling water pipe of feed pump a big vibration and noise and adjustment gate damage. In addition, the motor of the pump has a big vibration and the coil temperature reaches to 100 ℃ in summer.
To solve these issues, we decide to adopt variable frequency technology to adjust the speed of condensing pump and change the Q-H curve of the pump. The pressure is reduced at the same flow, so that the inlet gate opens, eliminating damper loss.
Technology
We choose to use 1000kW/6kV medium voltage AC drive produced by Shenzhen Gozuk Co Ltd. Capacity 1350kVA, ambience temperature 0 ℃-40 ℃.
Table 2 Parameters
Problems and Solutions
In order to reduce the cost of reform, we only change one of the two mutual-spare condensing pumps with variable frequency adjustment. Different adjustment modes makes different parameters between two pumps. So, there are following problems.
(1) The inlet gate opens when the pump runs in AC drive mode. It makes the condensing water pressure lower by changing the pump speed to adjust water level of deaerator, even not more than 1.6MPa. The water pressure declines with load reducing. The logic of " link start spare pump at low pressure " can not work, so after canceling this logic we increase water pressure alarm, that is, "condensing water pressure less than 1.0MPa or more than 1.8MPa" alarm, in the mean time, we cancel the logic of " link stop pump at low pressure" and " link start spare pump at low pressure ".
(2) For AC drive mode pump, condensation water pressure is low because of variable speed adjustment. But the constant speed pump is still adjusted by inlet gate whose water pressure is very high. In case of the variable frequency pump trips off, the pressure and flow increase suddenly when the spare pump starts, which will cause a big influence on the deaerator water level. For this issue, we change the control logic like this: when the AC drive pump or its switch trips off &sends command of link start constant speed pump, the program will sends a preset command to the inlet gate, shut down the inlet gate to a certain position immediately and program turns to "auto" to adjust deaerator water level.
(3) When the spare constant speed pump starts, pressure sudden-increase makes a big influence on other auxiliary equipments, especially to the system of mechanical seal cooling water, as its pressure should be less than 1.0Mpa. For this problem, we set a control logic which could prohibit closing adjustment gate when the pressure is too low or high, avoiding mechanical seal cooling water pressure too high caused by condensing water pressure sudden -increase. In normal operation, it adjusts automatically. At the same time, alarm "water pressure more than 0.8MPa or less than 0.5Mpa" is added.
(4) We add two water level gauges for deaerator water level, use their average to ensure the safety of automatic adjustment. The logic of water level signal is changed to "select two of three" when the water level is low, in order to prevent from pump mistake. When the AC drive mode pump runs in auto mode, the inlet gate could be controlled manually in remote, which increases the flexibility of the unit in startup, stop and low-load operation. "AC drive starts failure" alarm is added. Alarm includes all alarms, for more details in DCS.
Condensing system safety test
(1) In order to confirm the influence of AC drive pump trip-off and constant speed pump link-start, we make a load test for condensing pump before starting generator unit.
For AC drive mode pump, condensing water pressure is 1.19Mpa, flow is 737t/h, the opening of the deaerator inlet gate is 88.9%. Adjustment gate of mechanical seal cooling water of the feed pump transfers to auto operation, opening is 78.5% and pressure is 0.56Mpa. Load is set 150MW. Stop AC drive pump and constant speed pump link starts. Close opening of the inlet gate to 18.7% and transfer it into"automatic". Condensation water flow changes to 630t/h. Close the opening of mechanical seal cooling water gate to 22%. The minimum pressure can be down to 0.24Mpa, max can reach to1.2Mpa then settle to 0.4Mpa. The whole variety process is less than 30s. From the above test data we consider it can satisfy the basic operational requirements.
(2) Operating Parameters
Table 3 Typical operating parameters
PS: The water in table is mechanical seal cooling water of feed pump.
Table 4 Vibration values
The economic effects comparison
To ensure the economy of the reform, make the power consumption test both in frequency adjustment and throttle adjustment for the same condensing pump in 300MW, 200MW, 150MW load.
Table 5 Typical operating conditions comparison
From above data, AC drive could greatly reduce power consumption, especially in low load(in 150MW, 631.5kW can be saved, in 300MW, 470.7kW can be saved). After the reform, according to average load is 68.09% (204.27MW) and work time 7047h, 4306.4217MWh can be saved. Electrovalence is 0.32 yuan/kW.h, so annual saving is 1378000yuan (USD 202647). Through calculating, single unit power consumption rate could be reduced 0.3%.
The operation after reform
The variable frequency pump works and constant speed pump is only for spare. In order to ensure the safety of pumps and other auxiliary equipments, we make following measures:
(1) In general, variable frequency pump works and constant speed pump is only for spare. Opening of the inlet gate is between 80%—95%. Adjust the deaerator water level by AC drive. Turn down the inlet gate in low load to keep the pressure not less than 1.1 Mpa and speed not lower than 900r/m. Ensurethe other equipments run safely.
(2) Make periodical test for constant speed pump and the test should not be less than 2h to ensure excellent status. Make switch test for consdensate pumps every month.
(3) When we switch AC drive mode to constant speed mode, the deaerator inlet gate transfers to "auto". Accelerate AC drive pump to rated speed, and start constant speed pump, then stop the AC drive pump after checking normally. When the constant speed pump is running, adjust the AC drive pump runs in rated speed. Constant speed pump stops. Then adjust the speed of AC drive pump until the inlet gate opens large. Switch off "auto adjustment" of inlet gate. AC drive plunges to "auto adjustment".
(4) When the unit starts or stops, adjust AC drive speed in a certain value and adopt the inlet gate adjustment, which not only keeps the water level stable but also could make sure enough pressure cooling water for other auxiliary equipments. The AC drive pump has a large vibration in 600—800r/m. It may be the critical speed area, therefore, the AC drive pump is strictly prohibited to run in this area.
Conclusion
(1) The reform is safe and reliable. It reduces the vibration of condensing water pipeline and temperature of motor coil.
(2) The reform cancels throttle adjustment. Energy-saving for the condensing pump is obvious.
(3) Personnel must take care in checking , especially for maintenance and check of AC drive.
The total capacity is 8 × 300MW. Steam turbine unit is produced by Dongfang factory. The condensing system of 5, 6, 7, 8 are medium pressure system, equipped with 9LDTNA-5UA-type condensing pump made by Shenyang pump factory. The motor YLST500-4 type is made by Xiangtan Electrical Machinery Factory.
Condensing pump parameters and diagram
Flow | Lift | Power | Voltage | Current | Speed |
950m3/h | 280m | 1000kW | 6kV | 118.8A | 1480r/m |
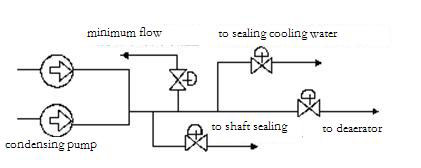
The condensing water mainly keeps the stability of deaerator water level by adjusting inlet gate, supplies mechanical seal cooling water to pump, low pressure axletree of steam turbine and other auxiliary equipments, also to other low pressure bypass, spray cylinder, the cold water tank inside.
Purpose
(1) The condensing water is medium pressure system. The pressure is not lower than 2.6Mpa when load is 300MW. Pressure is higher when opening is small during low load operation, which causes higher pressure. Gate opening control causes low economy. Even at full load, the opening is only about 30%, and much smaller at low-load.
(2) The high pressure condensing water causes the pipe a big vibration, the minimum flow adjustment gate leakage, meanwhile, makes the cooling water pipe of feed pump a big vibration and noise and adjustment gate damage. In addition, the motor of the pump has a big vibration and the coil temperature reaches to 100 ℃ in summer.
To solve these issues, we decide to adopt variable frequency technology to adjust the speed of condensing pump and change the Q-H curve of the pump. The pressure is reduced at the same flow, so that the inlet gate opens, eliminating damper loss.
Technology
We choose to use 1000kW/6kV medium voltage AC drive produced by Shenzhen Gozuk Co Ltd. Capacity 1350kVA, ambience temperature 0 ℃-40 ℃.
Table 2 Parameters
Rated input voltage | Input frequency | Output frequency | Rated output current | Acceleration/Deceleration time | AC Drive Efficiency |
6000V±10% | 45-50Hz | 0-50 Hz | 130A | 0.1-3000S | Rated load >96% |
Problems and Solutions
In order to reduce the cost of reform, we only change one of the two mutual-spare condensing pumps with variable frequency adjustment. Different adjustment modes makes different parameters between two pumps. So, there are following problems.
(1) The inlet gate opens when the pump runs in AC drive mode. It makes the condensing water pressure lower by changing the pump speed to adjust water level of deaerator, even not more than 1.6MPa. The water pressure declines with load reducing. The logic of " link start spare pump at low pressure " can not work, so after canceling this logic we increase water pressure alarm, that is, "condensing water pressure less than 1.0MPa or more than 1.8MPa" alarm, in the mean time, we cancel the logic of " link stop pump at low pressure" and " link start spare pump at low pressure ".
(2) For AC drive mode pump, condensation water pressure is low because of variable speed adjustment. But the constant speed pump is still adjusted by inlet gate whose water pressure is very high. In case of the variable frequency pump trips off, the pressure and flow increase suddenly when the spare pump starts, which will cause a big influence on the deaerator water level. For this issue, we change the control logic like this: when the AC drive pump or its switch trips off &sends command of link start constant speed pump, the program will sends a preset command to the inlet gate, shut down the inlet gate to a certain position immediately and program turns to "auto" to adjust deaerator water level.
(3) When the spare constant speed pump starts, pressure sudden-increase makes a big influence on other auxiliary equipments, especially to the system of mechanical seal cooling water, as its pressure should be less than 1.0Mpa. For this problem, we set a control logic which could prohibit closing adjustment gate when the pressure is too low or high, avoiding mechanical seal cooling water pressure too high caused by condensing water pressure sudden -increase. In normal operation, it adjusts automatically. At the same time, alarm "water pressure more than 0.8MPa or less than 0.5Mpa" is added.
(4) We add two water level gauges for deaerator water level, use their average to ensure the safety of automatic adjustment. The logic of water level signal is changed to "select two of three" when the water level is low, in order to prevent from pump mistake. When the AC drive mode pump runs in auto mode, the inlet gate could be controlled manually in remote, which increases the flexibility of the unit in startup, stop and low-load operation. "AC drive starts failure" alarm is added. Alarm includes all alarms, for more details in DCS.
Condensing system safety test
(1) In order to confirm the influence of AC drive pump trip-off and constant speed pump link-start, we make a load test for condensing pump before starting generator unit.
For AC drive mode pump, condensing water pressure is 1.19Mpa, flow is 737t/h, the opening of the deaerator inlet gate is 88.9%. Adjustment gate of mechanical seal cooling water of the feed pump transfers to auto operation, opening is 78.5% and pressure is 0.56Mpa. Load is set 150MW. Stop AC drive pump and constant speed pump link starts. Close opening of the inlet gate to 18.7% and transfer it into"automatic". Condensation water flow changes to 630t/h. Close the opening of mechanical seal cooling water gate to 22%. The minimum pressure can be down to 0.24Mpa, max can reach to1.2Mpa then settle to 0.4Mpa. The whole variety process is less than 30s. From the above test data we consider it can satisfy the basic operational requirements.
(2) Operating Parameters
Table 3 Typical operating parameters
Load MW | Current A | Speed r/m | Flow t/h | Condensation Pressure MPa | Cooling water Opening % | Cooling water pressure MPa | Adjustment gate opening% |
150 | 15 | 818 | 386 | 0.78 | 100 | 0.48 | 60.2 |
150 | 76 | 1490 | 397 | 3.05 | 49 | 0.66 | 32 |
200 | 23 | 926 | 497 | 0.98 | 100 | 0.60 | 57.6 |
200 | 81 | 1490 | 514 | 2.98 | 50 | 0.66 | 35.8 |
300 | 50.5 | 1188 | 743 | 1.53 | 75.2 | 0.66 | 47 |
300 | 92 | 1490 | 760 | 2.74 | 53 | 0.66 | 37.4 |
Table 4 Vibration values
Measurement site | Upper bracket (µm) | Lower bracket (µm) | ||||||
Speed(r/m) | Left | Front | Right | Behind | Left | Front | Right | Behind |
600 | 54 | 38 | 54 | 38 | 20 | 18 | 20 | 19 |
780 | 136 | 75 | 135 | 70 | 35 | 20 | 30 | 20 |
810 | 56 | 51 | 56 | 51 | 39 | 35 | 39 | 35 |
900 | 64 | 44 | 65 | 54 | 16 | 18 | 19 | 17 |
1200 | 55 | 15 | 50 | 15 | <20 | <15 | <20 | <15 |
Vertical vibration is 15µm |
The economic effects comparison
To ensure the economy of the reform, make the power consumption test both in frequency adjustment and throttle adjustment for the same condensing pump in 300MW, 200MW, 150MW load.
Table 5 Typical operating conditions comparison
Load MW | Flow t/h | Speed r/m | Current A | Power kW | Condensation Water Pressure | |||||
|
VS | CS | VS | CS | VS | CS | VS | CS | VS | CS |
150 | 386 | 395 | 818 | 1490 | 15 | 75 | 173 | 804.5 | 0.78 | 3.05 |
200 | 497 | 511 | 926 | 1490 | 23 | 80 | 251.8 | 862.9 | 0.98 | 2.98 |
300 | 743 | 737 | 1188 | 1490 | 50.5 | 92 | 521 | 991.7 | 1.53 | 2.8 |
From above data, AC drive could greatly reduce power consumption, especially in low load(in 150MW, 631.5kW can be saved, in 300MW, 470.7kW can be saved). After the reform, according to average load is 68.09% (204.27MW) and work time 7047h, 4306.4217MWh can be saved. Electrovalence is 0.32 yuan/kW.h, so annual saving is 1378000yuan (USD 202647). Through calculating, single unit power consumption rate could be reduced 0.3%.
The operation after reform
The variable frequency pump works and constant speed pump is only for spare. In order to ensure the safety of pumps and other auxiliary equipments, we make following measures:
(1) In general, variable frequency pump works and constant speed pump is only for spare. Opening of the inlet gate is between 80%—95%. Adjust the deaerator water level by AC drive. Turn down the inlet gate in low load to keep the pressure not less than 1.1 Mpa and speed not lower than 900r/m. Ensurethe other equipments run safely.
(2) Make periodical test for constant speed pump and the test should not be less than 2h to ensure excellent status. Make switch test for consdensate pumps every month.
(3) When we switch AC drive mode to constant speed mode, the deaerator inlet gate transfers to "auto". Accelerate AC drive pump to rated speed, and start constant speed pump, then stop the AC drive pump after checking normally. When the constant speed pump is running, adjust the AC drive pump runs in rated speed. Constant speed pump stops. Then adjust the speed of AC drive pump until the inlet gate opens large. Switch off "auto adjustment" of inlet gate. AC drive plunges to "auto adjustment".
(4) When the unit starts or stops, adjust AC drive speed in a certain value and adopt the inlet gate adjustment, which not only keeps the water level stable but also could make sure enough pressure cooling water for other auxiliary equipments. The AC drive pump has a large vibration in 600—800r/m. It may be the critical speed area, therefore, the AC drive pump is strictly prohibited to run in this area.
Conclusion
(1) The reform is safe and reliable. It reduces the vibration of condensing water pipeline and temperature of motor coil.
(2) The reform cancels throttle adjustment. Energy-saving for the condensing pump is obvious.
(3) Personnel must take care in checking , especially for maintenance and check of AC drive.
Post a Comment:
You may also like: