Category
- Products
-
- FAQ
- Contact us
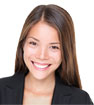
AC Drive Manufacturer
Considerations of changing DC drive to AC drive system
There are benefits to going AC (from an original DC application), but there can also be significant drawbacks. How much each weighs into the equation is based in part on the existing infrastructure and how "malleable" it is to change, how much physical space you have to install the new equipment, and how long your process line can afford to be down.
It is highly probable that the existing DC system is along the lines of a direct-drive installation - which means the motor shaft and the driven equipment shafts are rotating at the same speed. In part this is because DC has been limited by the brush/commutator interface speeds and the ability to transfer current... and in part due to the mechanical responsiveness of an ungeared system.
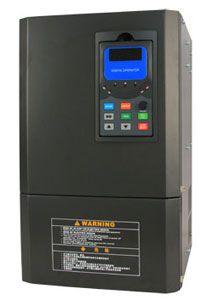
For a new AC application: look at the relative footprint of the drives. Compare cooling requirements - and incoming power requirements. Check communication protocols and the ability to interface with the existing process line controls. On the motor side, look at the machine footprint and shaft height. What about speed - is a gear required? How about cooling? Most of all - what about responsiveness to changes in the process?
Not all AC solutions are created equal. If the intent is to arrive at the same torque output at the motor shaft, the chances are good that the AC motor will take up more volume than the equivalent DC rating. And not all AC machines are created equal: sometimes a squirrel cage induction machine is more cost-effective, sometimes a wound-rotor induction is the better bet, and sometimes a synchronous design is the best choice. And sometimes (believe it or not) the good old DC equipment is the right tool for the job.
If the existing system is running (even badly) then I would measure Amps and Volts over the full range of operation of the system. This will tell you power and should also give you an indication where on the motor curve you are operating and how far into the field weakening area of the curve the system moves. You need to measure speed as well, you need this to figure out how much torque the new system needs to deliver and at what speed. With this info you will be able to pick a suitable motor - power and pole count and whether you need external cooling. This is the time to pick the cooling arrangement of the motor (sealed, forced air, water, etc.), remember to order the terminal box on the side of the motor that works best. Everything on a large motor is custom built and very hard to change later. Also, depending on size, choose any "extra" features you want (thermocouples for windings, bearings and lube oil).
Your mechanical engineer is going to be very concerned about matching shaft diameter and shaft height. Shaft diameter can be adapted by changing one half of the coupling to suit. Remember to purchase the coupling.
Your civil guy is going to want to know if the new machine will fit on the same foundations as the old one. You may need to build a sub-frame to adapt the old foundation to the new machine.
If your machine is big and you are on a weak supply then look at 12, 18 or 24 pulse converters. Be careful how you tune the new drive because AC drives can respond way quicker than DC drives and this can lead to mismatched response times with existing equipment or other instabilities. To get true DC performance you may need to install an encoder (a must on hoist applications). Cabling needs to be proper variable frequency drive cable or your new installation may not play nicely with the existing equipment - especially instrumentation.
It is highly probable that the existing DC system is along the lines of a direct-drive installation - which means the motor shaft and the driven equipment shafts are rotating at the same speed. In part this is because DC has been limited by the brush/commutator interface speeds and the ability to transfer current... and in part due to the mechanical responsiveness of an ungeared system.
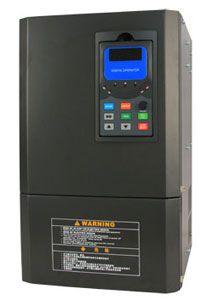
For a new AC application: look at the relative footprint of the drives. Compare cooling requirements - and incoming power requirements. Check communication protocols and the ability to interface with the existing process line controls. On the motor side, look at the machine footprint and shaft height. What about speed - is a gear required? How about cooling? Most of all - what about responsiveness to changes in the process?
Not all AC solutions are created equal. If the intent is to arrive at the same torque output at the motor shaft, the chances are good that the AC motor will take up more volume than the equivalent DC rating. And not all AC machines are created equal: sometimes a squirrel cage induction machine is more cost-effective, sometimes a wound-rotor induction is the better bet, and sometimes a synchronous design is the best choice. And sometimes (believe it or not) the good old DC equipment is the right tool for the job.
If the existing system is running (even badly) then I would measure Amps and Volts over the full range of operation of the system. This will tell you power and should also give you an indication where on the motor curve you are operating and how far into the field weakening area of the curve the system moves. You need to measure speed as well, you need this to figure out how much torque the new system needs to deliver and at what speed. With this info you will be able to pick a suitable motor - power and pole count and whether you need external cooling. This is the time to pick the cooling arrangement of the motor (sealed, forced air, water, etc.), remember to order the terminal box on the side of the motor that works best. Everything on a large motor is custom built and very hard to change later. Also, depending on size, choose any "extra" features you want (thermocouples for windings, bearings and lube oil).
Your mechanical engineer is going to be very concerned about matching shaft diameter and shaft height. Shaft diameter can be adapted by changing one half of the coupling to suit. Remember to purchase the coupling.
Your civil guy is going to want to know if the new machine will fit on the same foundations as the old one. You may need to build a sub-frame to adapt the old foundation to the new machine.
If your machine is big and you are on a weak supply then look at 12, 18 or 24 pulse converters. Be careful how you tune the new drive because AC drives can respond way quicker than DC drives and this can lead to mismatched response times with existing equipment or other instabilities. To get true DC performance you may need to install an encoder (a must on hoist applications). Cabling needs to be proper variable frequency drive cable or your new installation may not play nicely with the existing equipment - especially instrumentation.
Post a Comment:
You may also like: