Category
- Products
-
- FAQ
- Contact us
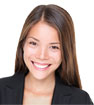
AC Drive Manufacturer
Home » Applications » Medium voltage AC drives in fans & pumps of power generators
Medium voltage AC drives in fans & pumps of power generators
Medium voltage AC drives are applied in generators of 100~600MW. Main equipment is PA fan, ID fan, FD fan and condensing pump.
Economic benefit
PA fan of #8 boiler (300MW)
PA fan of #8 boiler is equipped with 6 coal grinders. PA fan model of #7 and #8 is same. When plant made test, #7 boiler had not installed AC drive. Compared with #7, fan power of #8 boiler reduces power 1127 kW, 946 kW, 689 kW and 809kW in load of 150MW, 200MW, 250MW and 300MW. As per average load 200MW, yearly work time 7200h, power price 0.3yuan/ kW•h, we get that yearly power saved of PA fan is 6660000kW.h, equivalent to 2 million Yuan (USD 294117). Energy saving is more evident during low load operation. The investment can recover within 3 years.
ID fan of #2 boiler (100MW)
Model of #2 ID fan is Y4-73-11. Motor power is 550 kW. According to tests in different loads: compared with damper control, variable frequency input power reduces 471 kW, 506 kW, 472 kW and 428 kW in load of 50MW, 70MW, 85MW and 100 MW. As per yearly work time 6500h, power saved is 3140000kW.h, equivalent to 880000yuan (USD 129411). Investment can recover within 3.6 years.
Condensing pump of #6 generator (300MW)
After reconstruction of #6 condensing pump, compared with constant speed throttling control, AC drive saves 4080000kW.h. Deducting power consumption of air conditioner, yearly power saved is 4050000kW.h. As per power price 0.3yuan/ kW•h, 1250000yuan (USD183823) is saved in a year. Investment can recover within 3 years. So far, condensing pumps of #5, #6, #7 and #8 have been equipped with AC drive.
ID fan of #2 generator (125MW)
Motor power is 1000kW. System put into service in November, 2002. Compared with damper control, variable frequency input power reduces 571 kW, 472 kW, 489 kW and 520 kW in load of 90MW, 100MW, 110MW and 125 MW. As per yearly work time 5500h, yearly power saved is 2640000kW.h, equivalent to 860000yuan (USD 126470). The investment can recover within 2.8 years.
ID fan of #3 generator (250MW)
Plant made AC drive reconstruction for #3 ID fan during downtime. According to test, compared with damper control, variable frequency system reduces input power 1048 kW, 1062kW, 1052 kW, 872kW, 694kW and 520 kW in load of 126MW, 150MW, 175MW, 200MW, 225MW and 250MW. Yearly power saved is 6 million kW.h, equivalent to 1700000yuan (USD250000). The investment can recover within 2.6~2.8years.
ID fan of #3 boiler (200MW)
Before AC drive reconstruction, consumption of ID fan is 3.2~3.4 kW•h/t (steam). After reconstruction, it is 2.5kW•h /t (steam). As per yearly work time 7500h, yearly power saved is 3million kW.h. Investment can recover within 3.6~3.7 years.
PA fan of #3 boiler (600MW)
ID fan adopts AB Powerflex7000 AC drive. According to operation, power consumption of #3 fan is 0.47% which lowers 0.17% than before. Power consumption reduces 650000kW.h than #4 fan. Yearly power saved is 6 million kW.h.
Main problems during operation
There are several problems which should be pay attention during AC drive installation, commissioning and operation, such as control board fault, high impulse over voltage, high temperature, tandem axle and so on. These problems are being researched and improved.
Conclusion
Power plant should realize its society responsibility, take energy saving and emission reduction as internal dynamic of sustainable & healthy development. Plant should put energy saving into agenda, promote energy saving by new material, new technics and technology development.
Economic benefit
PA fan of #8 boiler (300MW)
PA fan of #8 boiler is equipped with 6 coal grinders. PA fan model of #7 and #8 is same. When plant made test, #7 boiler had not installed AC drive. Compared with #7, fan power of #8 boiler reduces power 1127 kW, 946 kW, 689 kW and 809kW in load of 150MW, 200MW, 250MW and 300MW. As per average load 200MW, yearly work time 7200h, power price 0.3yuan/ kW•h, we get that yearly power saved of PA fan is 6660000kW.h, equivalent to 2 million Yuan (USD 294117). Energy saving is more evident during low load operation. The investment can recover within 3 years.
ID fan of #2 boiler (100MW)
Model of #2 ID fan is Y4-73-11. Motor power is 550 kW. According to tests in different loads: compared with damper control, variable frequency input power reduces 471 kW, 506 kW, 472 kW and 428 kW in load of 50MW, 70MW, 85MW and 100 MW. As per yearly work time 6500h, power saved is 3140000kW.h, equivalent to 880000yuan (USD 129411). Investment can recover within 3.6 years.
Condensing pump of #6 generator (300MW)
After reconstruction of #6 condensing pump, compared with constant speed throttling control, AC drive saves 4080000kW.h. Deducting power consumption of air conditioner, yearly power saved is 4050000kW.h. As per power price 0.3yuan/ kW•h, 1250000yuan (USD183823) is saved in a year. Investment can recover within 3 years. So far, condensing pumps of #5, #6, #7 and #8 have been equipped with AC drive.
ID fan of #2 generator (125MW)
Motor power is 1000kW. System put into service in November, 2002. Compared with damper control, variable frequency input power reduces 571 kW, 472 kW, 489 kW and 520 kW in load of 90MW, 100MW, 110MW and 125 MW. As per yearly work time 5500h, yearly power saved is 2640000kW.h, equivalent to 860000yuan (USD 126470). The investment can recover within 2.8 years.
ID fan of #3 generator (250MW)
Plant made AC drive reconstruction for #3 ID fan during downtime. According to test, compared with damper control, variable frequency system reduces input power 1048 kW, 1062kW, 1052 kW, 872kW, 694kW and 520 kW in load of 126MW, 150MW, 175MW, 200MW, 225MW and 250MW. Yearly power saved is 6 million kW.h, equivalent to 1700000yuan (USD250000). The investment can recover within 2.6~2.8years.
ID fan of #3 boiler (200MW)
Before AC drive reconstruction, consumption of ID fan is 3.2~3.4 kW•h/t (steam). After reconstruction, it is 2.5kW•h /t (steam). As per yearly work time 7500h, yearly power saved is 3million kW.h. Investment can recover within 3.6~3.7 years.
PA fan of #3 boiler (600MW)
ID fan adopts AB Powerflex7000 AC drive. According to operation, power consumption of #3 fan is 0.47% which lowers 0.17% than before. Power consumption reduces 650000kW.h than #4 fan. Yearly power saved is 6 million kW.h.
Main problems during operation
There are several problems which should be pay attention during AC drive installation, commissioning and operation, such as control board fault, high impulse over voltage, high temperature, tandem axle and so on. These problems are being researched and improved.
Conclusion
Power plant should realize its society responsibility, take energy saving and emission reduction as internal dynamic of sustainable & healthy development. Plant should put energy saving into agenda, promote energy saving by new material, new technics and technology development.
Post a Comment:
You may also like: