Category
- Products
-
- FAQ
- Contact us
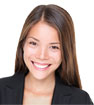
AC Drive Manufacturer
Why use AC Drives?
AC drives are one of the most effective tools managers can use to control a facility's energy use. As organizations struggle to curtail costs in every possible way, AC drive applications offer some of the best available returns on investment. Simple payback for an AC drive typically falls between six months and three years.
For years, managers have used variable frequency drives successfully for a range of applications, such as reducing energy use in fans, pumps, chillers, and cooling towers by up to 50 percent. While AC drives have proven effective in reducing energy use, technology advances are making them even more appealing.
Making a Match
A building's energy-using systems traditionally have enough capacity to meet the estimated peak load for that building, even though peak load typically occurs for no more than 1 percent of the annual hours of operation.
When a system operates at less than capacity, HVAC systems traditionally use a number of different devices to reduce the flow of air or water. This method of throttling output to match load requirements is effective in controlling the flow but is not the most energy-efficient strategy.
AC drives offer an alternative means of matching system output to load requirements by slowing the motors that drive HVAC system components. Unlike throttling, where a motor's energy use decreases only slightly with the decreasing system load, slowing a motor to match a decreased load results in a rapid drop-off in a motor's energy requirements.
New-Generation AC Drives Offer Constant Power Factor
Earlier-generation AC drives reduced energy use effectively, but they presented some drawbacks. One drawback was noise. When operating at reduced speeds, AC drives induced vibrations in motor laminations. These vibrations carried through piping, ductwork and the building structure, eventually affecting occupants. New-generation systems operate at higher frequencies, resulting in vibrations and noise that is not audible.
Another drawback to early-generation systems was their low power factor, particularly when operating at reduced motor speeds. A low power factor has a number of drawbacks for both facilities and utilities, including a reduction in the power-carrying capacity of electrical-distribution systems. If the capacity falls below a minimum predetermined value, the utility can impose penalties.
New-generation systems offer a nearly constant power factor at all operating speeds, eliminating the loss of system capacity and avoiding utility-imposed penalties.
Most new systems use pulse-width modulation, which converts incoming 60-cycle power to direct current. The direct current then switches rapidly and intermittently to produce pulses of varying-output voltages and widths. This mode of operation improves the process's overall efficiency compared to earlier systems, reduces losses in the device wiring, and reduces the formation of harmonic frequencies - all while providing better speed control.
Fans, Centrifugal Chillers are Common AC drive Applications
Manufacturers have designed AC drives for use with single- and three-phase induction motors. Three applications provide the greatest benefits: those that require or can benefit from variable-speed operation, those requiring precise speed control, and those requiring coordinated operation of multiple motors, such as on a bank of pumps operating in parallel.
In HVAC systems, one cost-effective applications of AC drives involves centrifugal chillers. These units typically operate at full-load capacity for less than 1 percent of annual operating hours. This capacity decreases during the remaining operating hours by partially closing inlet vanes to the compressor.
This mode of control effectively reduces chiller capacity, but it only slightly reduces energy requirements. In contrast, an AC drive reduces energy requirements dramatically.
Fan systems also are common applications for AC drives. Typical variable-volume systems use dampers and inlet vanes to match a fan's output to the building load. While these controls reduce fan energy use, an AC drive more accurately matches fan airflow to the building load, while producing even greater energy savings.
Finally, pumps also benefit from AC drives. Most pumps are constant-flow systems, regardless of the load. System flows match the building loads through some form of mechanical throttling, such as bypass or control valves installed at individual devices. As a result, the pumping system's energy requirements remain relatively constant, regardless of the load.
AC drives can match the system's flow to the load requirements, reducing energy use and the stress on the pumps. Typical pumping systems that can benefit from the use of AC drives include hydronic heating and air conditioning, chiller-condenser water, central domestic hot water, and domestic water-pressure boosters.
AC Drives Reduce Maintenance, Extend Motor Life
While managers most often cite energy management as the reason for installing an AC drive, the technology offers other significant benefits, including reduced motor and variable frequency drive maintenance and longer motor life. When a motor connected to a load starts, the current it draws typically is much greater than the current it draws at full load. During repeated start-stop cycles over the motor's operating life, this in-rush current causes heating and stress in the motor's windings, and it can damage them and lead to motor failure.
AC drives control motor start-up by initially applying a very low frequency and voltage to the motor. The voltage and frequency ramp up at a controlled rate, greatly reducing the in-rush current, as well as heat and stress on motor windings, thereby extending motor life.
Finally, AC drives reduce maintenance costs. Heat is a natural enemy of electrical components, and high in-rush currents cause heating and stress in motor starters, cables, contacts, and connectors, which can lead to pitting, corrosion, and insulation breakdown. AC drives limit the in-rush current by using soft-start technology, preventing stress on these components and keeping motors operating longer.
For years, managers have used variable frequency drives successfully for a range of applications, such as reducing energy use in fans, pumps, chillers, and cooling towers by up to 50 percent. While AC drives have proven effective in reducing energy use, technology advances are making them even more appealing.
Making a Match
A building's energy-using systems traditionally have enough capacity to meet the estimated peak load for that building, even though peak load typically occurs for no more than 1 percent of the annual hours of operation.
When a system operates at less than capacity, HVAC systems traditionally use a number of different devices to reduce the flow of air or water. This method of throttling output to match load requirements is effective in controlling the flow but is not the most energy-efficient strategy.
AC drives offer an alternative means of matching system output to load requirements by slowing the motors that drive HVAC system components. Unlike throttling, where a motor's energy use decreases only slightly with the decreasing system load, slowing a motor to match a decreased load results in a rapid drop-off in a motor's energy requirements.
New-Generation AC Drives Offer Constant Power Factor
Earlier-generation AC drives reduced energy use effectively, but they presented some drawbacks. One drawback was noise. When operating at reduced speeds, AC drives induced vibrations in motor laminations. These vibrations carried through piping, ductwork and the building structure, eventually affecting occupants. New-generation systems operate at higher frequencies, resulting in vibrations and noise that is not audible.
Another drawback to early-generation systems was their low power factor, particularly when operating at reduced motor speeds. A low power factor has a number of drawbacks for both facilities and utilities, including a reduction in the power-carrying capacity of electrical-distribution systems. If the capacity falls below a minimum predetermined value, the utility can impose penalties.
New-generation systems offer a nearly constant power factor at all operating speeds, eliminating the loss of system capacity and avoiding utility-imposed penalties.
Most new systems use pulse-width modulation, which converts incoming 60-cycle power to direct current. The direct current then switches rapidly and intermittently to produce pulses of varying-output voltages and widths. This mode of operation improves the process's overall efficiency compared to earlier systems, reduces losses in the device wiring, and reduces the formation of harmonic frequencies - all while providing better speed control.
Fans, Centrifugal Chillers are Common AC drive Applications
Manufacturers have designed AC drives for use with single- and three-phase induction motors. Three applications provide the greatest benefits: those that require or can benefit from variable-speed operation, those requiring precise speed control, and those requiring coordinated operation of multiple motors, such as on a bank of pumps operating in parallel.
In HVAC systems, one cost-effective applications of AC drives involves centrifugal chillers. These units typically operate at full-load capacity for less than 1 percent of annual operating hours. This capacity decreases during the remaining operating hours by partially closing inlet vanes to the compressor.
This mode of control effectively reduces chiller capacity, but it only slightly reduces energy requirements. In contrast, an AC drive reduces energy requirements dramatically.
Fan systems also are common applications for AC drives. Typical variable-volume systems use dampers and inlet vanes to match a fan's output to the building load. While these controls reduce fan energy use, an AC drive more accurately matches fan airflow to the building load, while producing even greater energy savings.
Finally, pumps also benefit from AC drives. Most pumps are constant-flow systems, regardless of the load. System flows match the building loads through some form of mechanical throttling, such as bypass or control valves installed at individual devices. As a result, the pumping system's energy requirements remain relatively constant, regardless of the load.
AC drives can match the system's flow to the load requirements, reducing energy use and the stress on the pumps. Typical pumping systems that can benefit from the use of AC drives include hydronic heating and air conditioning, chiller-condenser water, central domestic hot water, and domestic water-pressure boosters.
AC Drives Reduce Maintenance, Extend Motor Life
While managers most often cite energy management as the reason for installing an AC drive, the technology offers other significant benefits, including reduced motor and variable frequency drive maintenance and longer motor life. When a motor connected to a load starts, the current it draws typically is much greater than the current it draws at full load. During repeated start-stop cycles over the motor's operating life, this in-rush current causes heating and stress in the motor's windings, and it can damage them and lead to motor failure.
AC drives control motor start-up by initially applying a very low frequency and voltage to the motor. The voltage and frequency ramp up at a controlled rate, greatly reducing the in-rush current, as well as heat and stress on motor windings, thereby extending motor life.
Finally, AC drives reduce maintenance costs. Heat is a natural enemy of electrical components, and high in-rush currents cause heating and stress in motor starters, cables, contacts, and connectors, which can lead to pitting, corrosion, and insulation breakdown. AC drives limit the in-rush current by using soft-start technology, preventing stress on these components and keeping motors operating longer.
Post a Comment:
You may also like: